Why the world needs to focus on Battery production?
- October 17, 2023
- Posted by: Anish
- Category: Feed
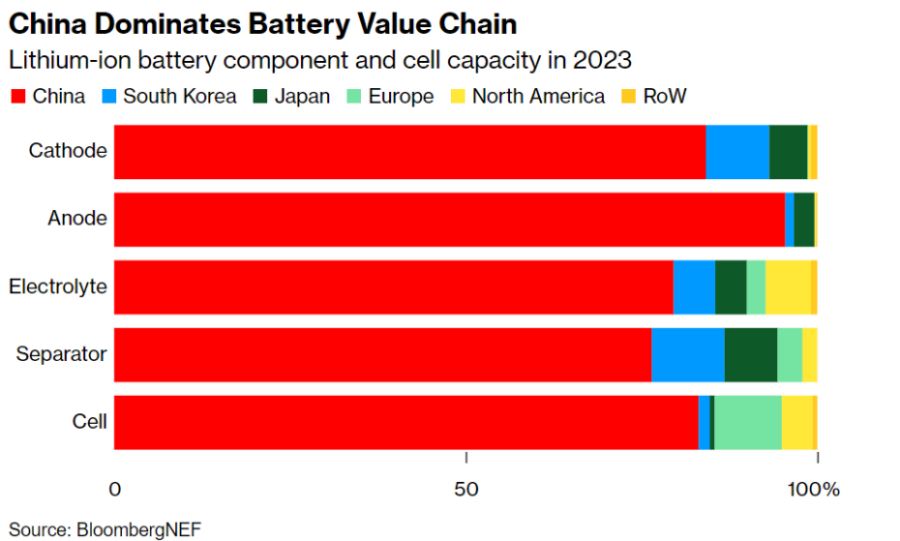
The rise of electric cars (EVs) is staggering. Over the past decade, Teslas have gone from being the car of the uber rich to the car of the Uber driver. All of the major automakers are taking the plunge on EVs, which is driving down prices and expanding available options. Globally, this year will see more than 14 million electric cars sold, compared with just 700,000 in 2016. And some 23 countries have now passed a crucial EV tipping point — 5% of new-car sales — after which adoption picks up dramatically. In China, the biggest Electric Vehicle (EV) market, 38% of new-car sales were electric in August 2023.
China’s dominance over the EV and battery supply chains has become a point of contention. Asia’s largest economy has a deep stranglehold on battery production, leaving global carmakers dependent at one point or another on Chinese partners. China’s battery makers supply some 80% of cells worldwide, backed by a mining and processing chain that increasingly resides in the country’s hands.
With the exception of graphite, mining is the area that’s least controlled by China, though the nation’s investment in South American/African lithium mines to Indonesian nickel producers still gives it a heave.
The next step — refining — is tougher to crack and China has spent years building its expertise. The country processes more than half the world’s lithium, two-thirds of its cobalt, more than 70% of its graphite and about one-third of its nickel, according to the International Energy Agency.
But where China truly flexes its might is in cell components — the four key parts that are essential for a battery to work. The Chinese state spent tens of billions of dollars in a decade to move to the Battery Energy Storage System (BESS) technology which we are all benefiting from.
It has about 70% of the world’s production capacity of cathodes (the part of the cell that receives electrons) and more than 80% of anodes (the part that releases electrons on discharge), and well over half of electrolyte and separator output. Those parts come together to make a lithium-ion battery, more than three quarters of which are made in China and mostly by just two firms — Contemporary Amperex Technology Co. Ltd. (CATL) and BYD Co.
That extensive manufacturing infrastructure, coupled with generous subsidies and other support that costs the government billions of dollars each year, has made China home to the biggest Battery Energy Storage System (BESS).
China’s battery packs come in at $127 per kilowatt hour on a volume-weighted average basis while prices in North America and Europe are 24% and 33% higher, according to Bloomberg.
That makes battery-cell factories the most capital-intensive part of the push to diversify supply chains and, while difficult to pin down the exact spending needed to break away from China, snapshots show how quickly those costs will pile up.
Just a single lithium-iron-phosphate battery factory would cost about $865 million to build in both the US and Germany, Europe’s biggest car market, according to calculations. That compares with $650 million in China, in large part due to the country’s lower construction and labour costs.
Taking a slightly broader view, Bloomberg data suggest that Europe and US would need to spend $98 billion and $82 billion, respectively, on the battery-metal refining to cell-making facilities they’d need by 2030. Battery cells and packs account for most of that cost, with mining raw materials and building and fitting out the factories to make the EVs themselves adding to the bill.
The Chinese based CATL is ramping up production at its battery-cell plant in Germany and is building another factory in Hungary. China’s SVolt Energy Technology Co. is set to expand its footprint in Europe to as many as five factories and is already in talks to supply the region’s carmakers with batteries.
India’s Vision for Battery Manufacturing:
Indian Energy Storage Alliance (IESA) has set a vision to further scale the battery manufacturing capacity to over 500 Giga-watt-hours (GWh) by 2035 considering the demand growth for both stationary storage and e-mobility in India.
‘India Battery Manufacturing Vision’, the country can generate over 2.6 million jobs and bring in USD 35 billion in investments by 2035.
IESA is anticipating that the first gigafactory (manufacturing facility that produces components linked to electrification and decarbonization technologies) in India will start commercial production in 2024 and installed manufacturing capacity of ACC (Advanced chemistry cell) batteries should scale to over 50 GWh by 2027-28.
Based on current announcements, Indian gigafactories should scale to over 150 GWh annual capacity by end of 2030.
In addition, there is a great opportunity for localising key components of gigafactories such as cathode-anode separator, electrolytes etc. With the need for alternate supply chain in developed markets such as US and European Union, he noted.
Indian battery supply chain industry could scale to over 1,000 GWh manufacturing capacity with enabling policy and regulatory framework.